Modulation

Laser modulation is a critical facet of laser technology, allowing for controlled variations in key parameters such as intensity, frequency, or phase. Such control opens the door to a broad range of scientific and commercial applications. Aerospace, automotive and biomedical industries all heavily rely on systems that use modulated lasers as a cornerstone of their technology. The modulation of laser output can be accomplished either directly or externally, each approach presenting its own set of drawbacks and advantages that merit discussion.
External Modulation
External modulation involves manipulating the laser beam outside the laser cavity. Acousto-optic and electro-optic modulators are commonly used for this purpose. They employ sound waves or electric fields to change the refractive index of a crystal through which the beam is passed, thereby enabling tunable frequency or optical output of the laser. While providing significant control over these parameters, external modulation introduces system complexity. Additional components can impact overall system cost and increase the risk of optical losses. Nevertheless, in applications where intricate adjustments are required, such as in interferometers and pulse generators, external modulation proves indispensable.
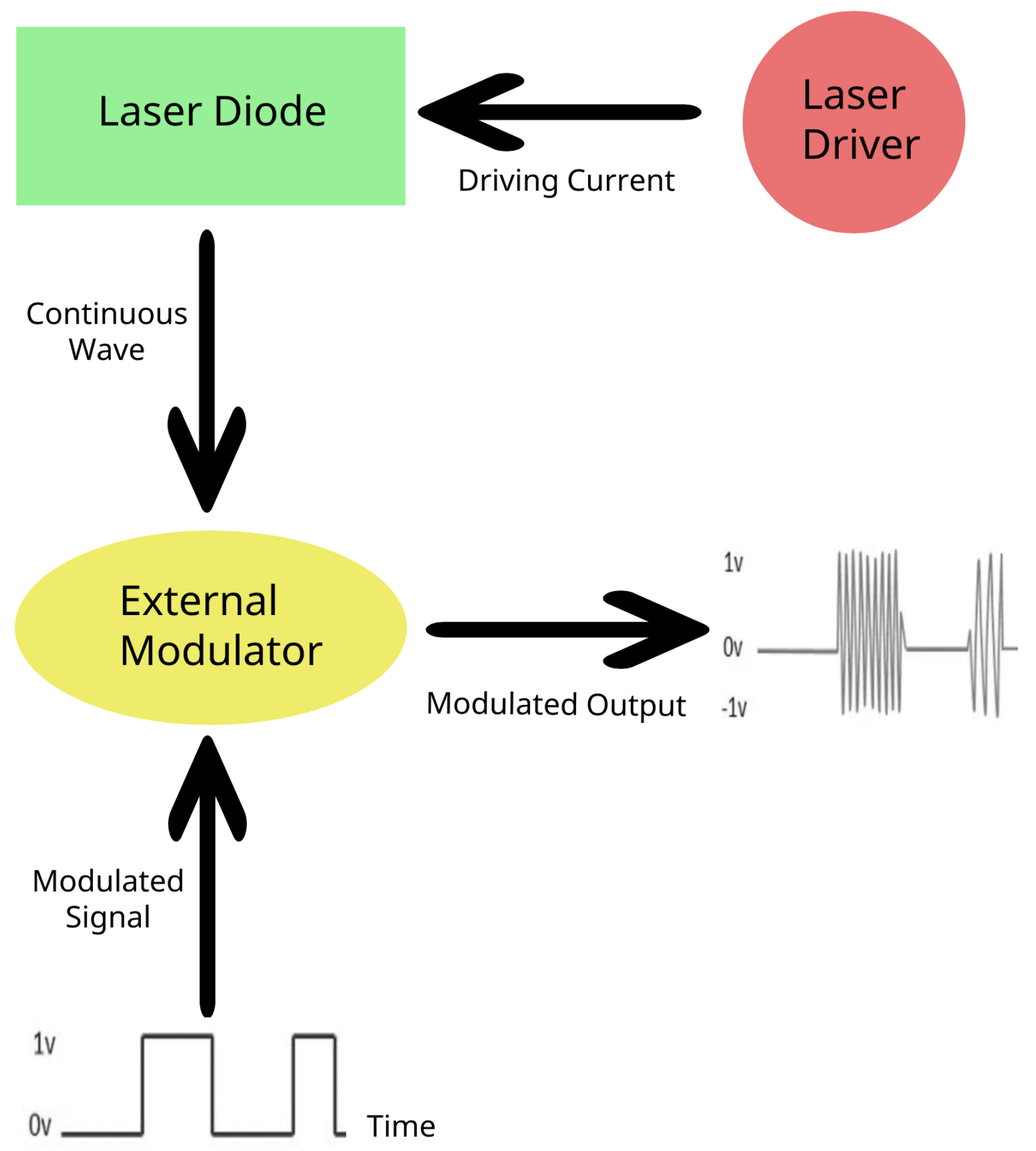
Figure 1. External modulation schematics.
Direct modulation entails the manipulation of the current passing through the laser diode. This is often achieved using a pulse width modulation signal generator. The signal is received by a Transistor-Transistor Logic (TTL) pin, and is interpreted by the laser diode controller which regulates the current passing through the diode. This method provides real-time control by rapidly switching the laser diode on and off. The simplicity and responsiveness of direct modulation make it a preferred choice in applications where rapid adjustments are essential, including flow cytometry and lidar. However, challenges arise when dealing with laser types that are limited by their internal circuitry or optical components.
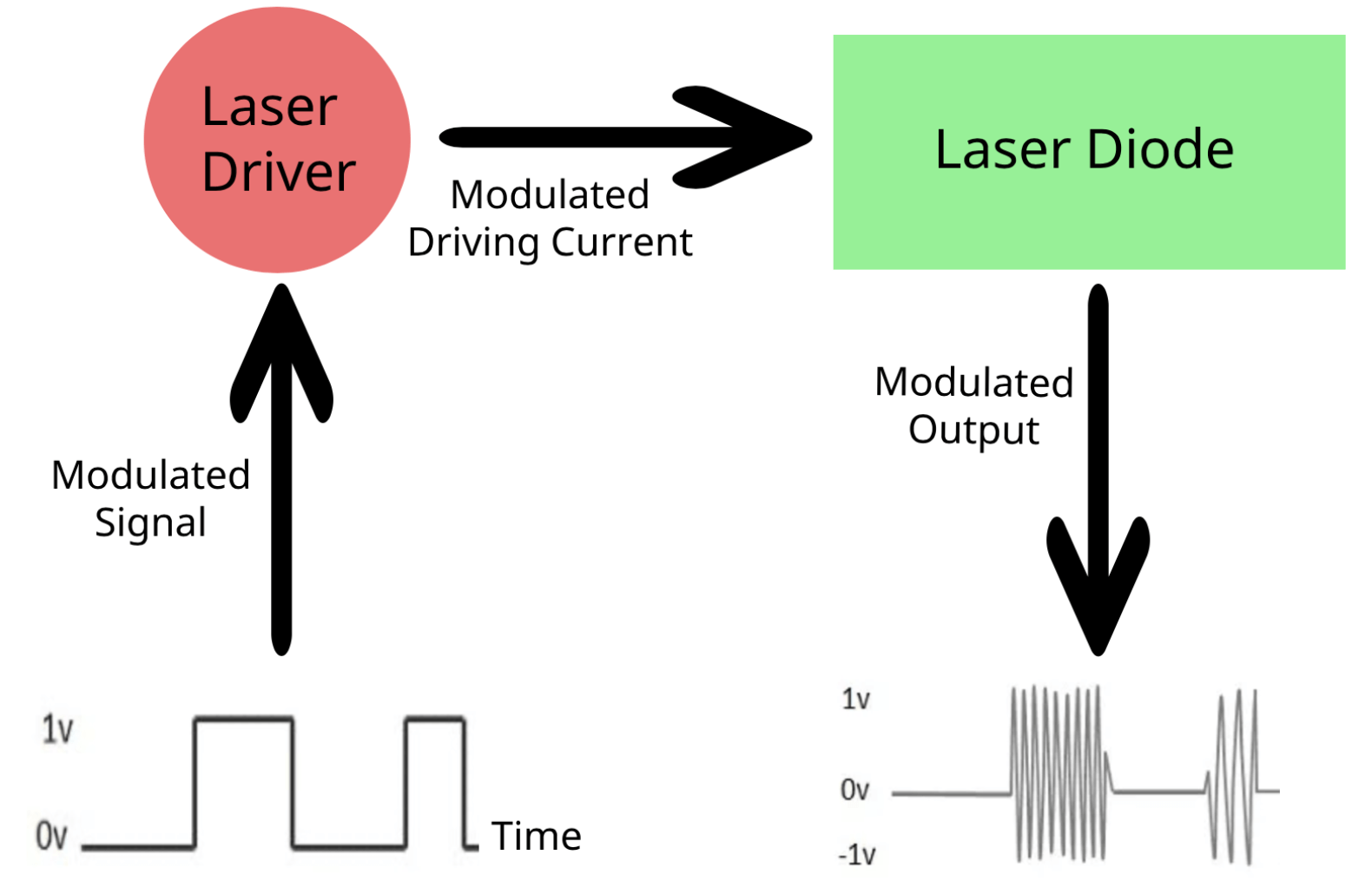
Figure 2. Direct modulation schematics.
Digital vs Analog Modulation
It is important to distinguish between two types of modulation outputs - analogue and digital. Analog modulation involves varying a parameter across a continuous spectrum, such as tuning the wavelength of the laser output between 404nm and 406nm. On the other hand, digital modulation entails the laser output alternating between two discrete values, like switching between on and off states. Both can be accomplished through direct and external methods. For instance, gradually decreasing the driving current of a laser diode can shift the wavelength. Similarly, changing the electric field applied to an electro-optic modulator changes the refractive index of the material and can shift the output wavelength. Understanding this distinction in modulated output is crucial for manipulating parameters effectively and selecting the optimal arrangement for your system.
Attainable Modulation Bandwidths: Duty Cycle, Rise and Fall Times
Modulation bandwidth refers to the range of frequencies over which a laser's output can be effectively varied. In other words, this is the shortest amount of time it takes to complete one on-off cycle. The proportion of time which the laser was in the “on” state is know as the duty cycle and it can be controlled to adjust the output power. It is linearly proportional, meaning that a 50% duty cycle would half the output power. One cycle can be characterized by a square pulse shape going from 0V to a set voltage and back. Key parameters characterizing one pulse are the rise and fall times (Figure 3.) . They are defined as the time taken for the laser intensity to go from 10% of the set value to 90% and vice versa. By dividing 1 by the sum of these values a maximum theoretical frequency of modulation can be obtained. In actually the maximum frequency will always be lower due to limitations of the system/hardware, measuring tools, and physical phenomena such as heating over prolonged use.
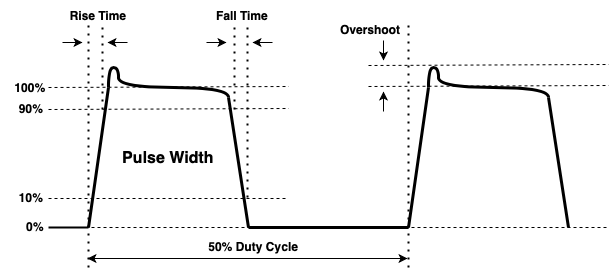
Figure 3. Illustration of the on-off cycle with key parameters annotated.
The bandwidth for direct modulation is mostly impacted by the electronics and optical components used in the laser system, with the slowest step being the limiting factor. Integrated Optics lasers operating in “automatic power control” (APC) mode use an internal photodiode which sends feedback to the diode controller to adjust the driving current in order to maintain a consistent power output. Compared to the “automatic current control” ACC mode, where the driving current is kept constant, the extra step limits the maximum modulation frequency. While our typical diode laser, set to ACC mode, can reliably operate at 10MHz, the use of APC mode, incorporating an internal photodiode for feedback, may reduces the maximum achievable modulation frequency by up to 1000 times (Figure 4.). However, the option to switch between these modes provides versatility and expands the applicability of our lasers to a variety of systems.
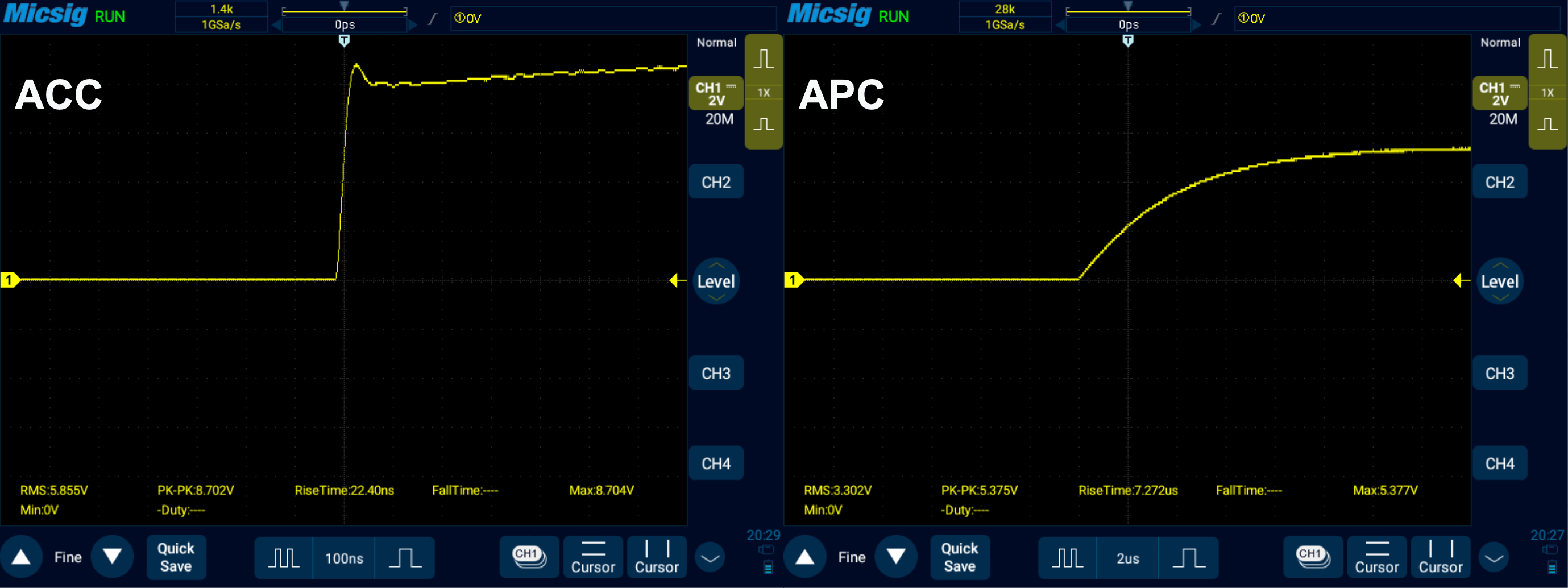
Figure 4. Rise times of our 505L-11A laser operating in ACC and APC modes. The rising edge of the pulse in ACC mode is much steeper, and therefore only takes 22 ns to reach 90% of the maximum value compared to 7272 ns in APC.
Limitations using DPSS Lasers
Diode-Pumped Solid-State (DPSS) lasers, utilize a semiconductor laser diode to pump a solid-state gain medium in order to emit light of wavelength normally unattainable by laser diodes alone. While valuable, this technology faces challenges with direct modulation. The crystal/gain medium acts as an energy storage, which takes time to charge, limiting the maximum frequency of modulation. Rapid switching introduces thermal fluctuations and optical noise, affecting the stability and coherence of the laser output. These issues can lead to relaxation oscillation and mode hopping which distort the shape of the laser pulse. These limitations can be overcome by using external modulators as they bypass the limiting internal mechanisms and modulate the beam after it has been generated.
Limitations using Single Longitudinal Mode Lasers
Single longitudinal mode (SLM) lasers, emitting a single, well-defined wavelength, exhibit heightened sensitivity to temperature fluctuations and the stability of the driving current. During direct modulation, where the laser rapidly alternates between on and off states, it does not receive a continuous and stable current but rather oscillates between a preset value and zero. This process also impacts the heat generated by the emitter within the diode and causes temperature fluctuations of both the diode and laser base temperature. Consequently, considerations such as mode hopping and the risk of laser diode emitter failure become significant in instances of direct modulation. The narrow line-width of single longitudinal mode lasers necessitates precise modulation management to prevent undesirable shifts in wavelength, particularly in applications where wavelength stability is critical, such as in high-precision measurements and spectroscopy. Similarly to DPPS lasers, incorporating external modulators may help bypass some of these limitations.
Understanding the intricacies of laser modulation techniques is imperative for informed decision-making in various applications. External modulation offers versatility at the expense of increased system complexity and cost, while direct modulation provides real-time control but poses challenges for certain laser types. Therefore, when a product or experimental set up requires laser modulation, especially with DPSS and SLM lasers, the aforementioned advantages and limitations ought to be considered.